Automated Sponge/Scrap Feeding Convey System
Streamlined Solution for Modern Steelmaking

As the steel industry in India increasingly relies on iron ore sponge, the need for efficient handling and feeding systems has become paramount. With the rising costs of recycled scrap, many steel plants now use sponge iron and pellets in melting ratios of up to 50%-80%. To address these challenges, ISC has developed a comprehensive, hassle-free Sponge Feeding System in collaboration with a renowned engineering consultancy firm. This system is designed to optimize the loading and feeding of sponge iron, ensuring consistent and efficient operation on the furnace floor.
- ISC GROUP
Semi-Auto Mode
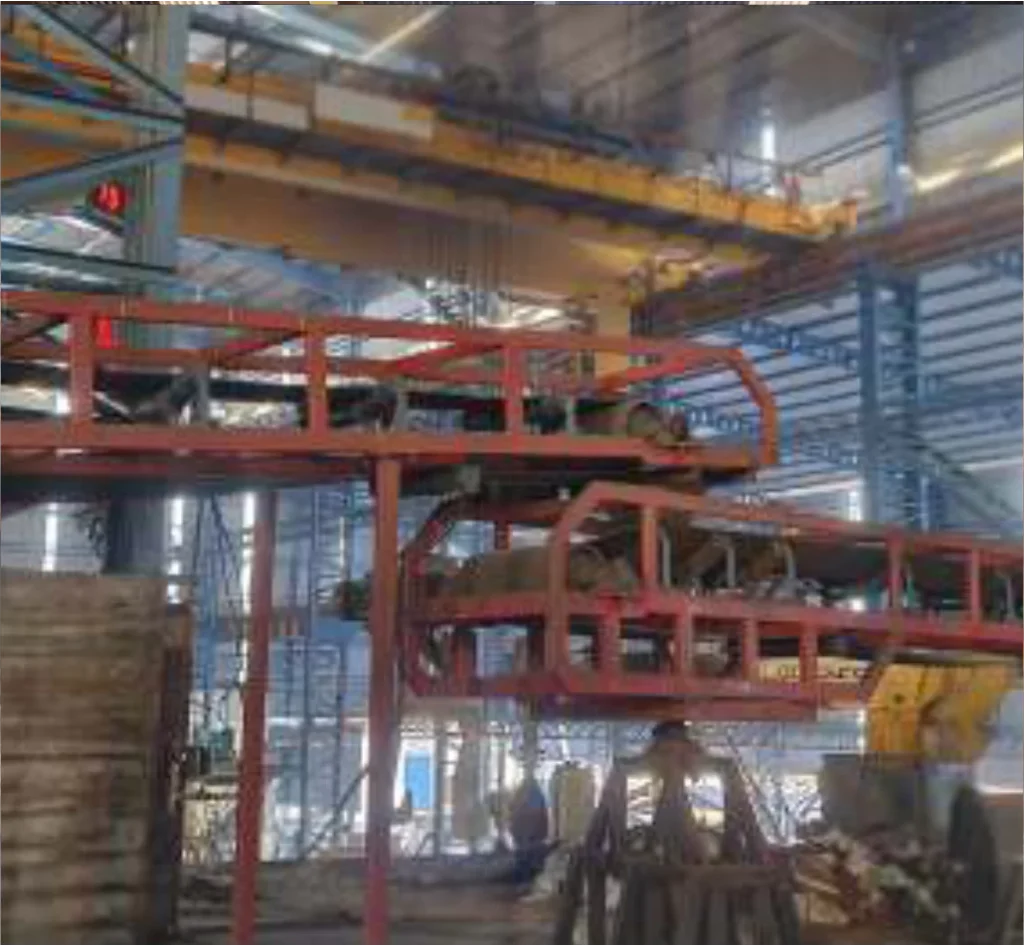
The semi-automatic mode of the system begins with a day hopper, where the client manually loads sponge iron onto the furnace floor using a magnet or grab. A PLC-based control system continuously monitors the quantity of sponge in the hopper, ensuring accurate measurement at all times. Key highlights of this mode include a hopper weighing system and a swiveling arrangement that facilitates feeding to two crucibles or conveyors for each crucible. This design eliminates the need for sponge storage in the SMS shed and keeps the furnace floor free from moving equipment, enhancing safety and operational efficiency.
In the full auto mode, sponge is loaded into the ground hopper via a payloader, magnet, or grab bucket. After an optional batching process, the sponge is charged into the system and conveyed to the furnace floor using a network of conveyors. On the furnace floor, the sponge is stored in day hoppers, allowing for efficient and continuous operation. This mode features two levels of automation, ensuring seamless integration into existing production processes. Key highlights include automatic weighing and batching of the sponge charge mix, which contributes to high-quality steel production and provides an accurate tally of operational material weight.
- ISC GROUP
Full Auto Mode
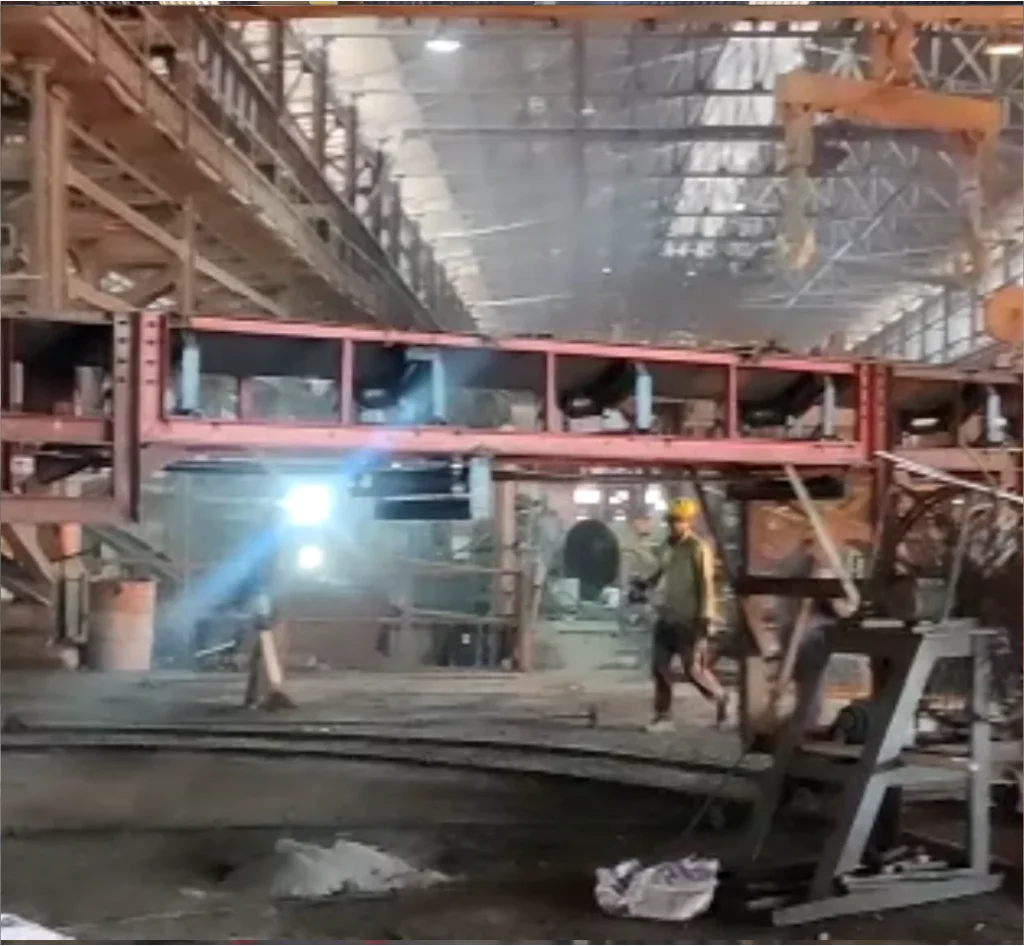